2.4 BALLASTING FACTORS
Selection of a ballasting arrangement is normally not an option for
the tanker's crew. The locations of the SBT or CBT tanks dictate where
ballast is to be carried. When additional ballast is carried because
of anticipated heavy weather, or because of ballast tank cleaning or
repairs, the following factors should be considered:
2.4.1 Stress on the hull
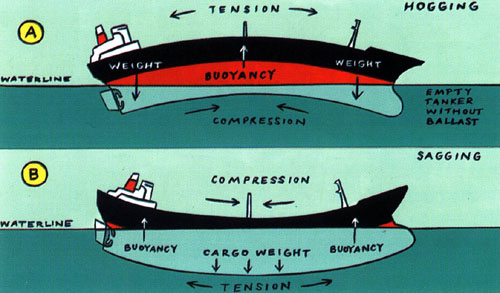
Hogging stresses induced in an empty, unballasted
tanker; sagging stresses arc induced in a tanker loaded to its mark.
The location of the ballast contributes to three kinds of stress on
the hull. An empty tanker is subject to bending stresses caused by the
relatively heavy structure at the bow and the stern, (where there is
less buoyancy), combined with the light structure and excess of buoyancy
amidship. An empty tanker is said to be 'hogged'.
The main deck is in tension, and the keel is compressed by this bending
force. Adding ballast to the midship area tanks reduces this bending
force. The midship ballast tank should be filled first to minimise stress
during ballasting. Likewise, the sequence of subsequent tank filling
should be selected to minimise hull stresses during the filling operation.
Shear stress is caused by uneven distribution of forces at adjacent
parts of the hull, such as at a transverse bulkhead separating a ballasted
tank from an empty one. The ballast pattern must not produce shear forces
which would exceed the yield point of the steel hull.
The calculation of bending and shear forces is complex for the designer.
This calculation has been simplified for the master/chief officer by
providing a set of stress moment tables or approved computer program.
The chief officer can quickly determine the stress numerals for a proposed
loading plan by using a customised computer program.
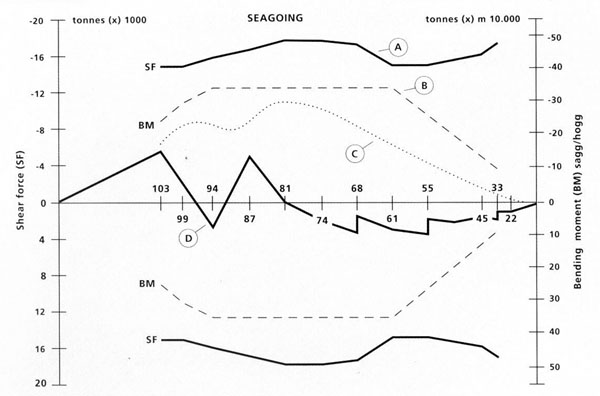
Example of computer plot of tanker stresses. A
Maximum allowed seagoing shear force. B Maximum allowed
bending moment (hogg). C Actual bending moment curve.
D actual shear force curve.
Each tanker must also be provided with a stability booklet, with which
an officer can calculate the stability and stresses of his ship using
only pencil and paper. The stability book is essential because computers
fail, and because they are most likely to be unavailable when a ship
is damaged, and a stability calculation is most needed.
Localised structural stresses are also produced by the ballast pattern.
In general, the longitudinal bulkheads of a tanker are more resistant
to outward force (due to the heavier wing tank framing), than to inward
pressure. It is better to ballast the centre tanks than the wing tanks.
Also, a 'checkerboard' ballast pattern tends to stress the brackets
in the ballasted tanks as it sets up a wave deflection pattern in the
longitudinal and transverse bulkheads.
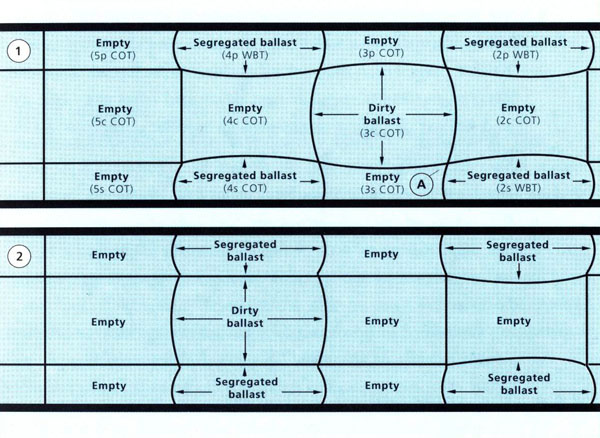
1 Undesirable ballast arrangement
- four additional bulkheads are placed under bending
stress and four corner intersections are heavily stressed (A - heavily
stressed bulkhead intersection). 2
Preferred ballast arrangement - provided
hull bending and shear stresses are within acceptable limits.
Where ballast will be changed during the voyage, the stability and
stress must be evaluated for each step of the procedure to ensure that
the maximum allowable at sea stress conditions will not be exceeded
while changing from one set of ballast tanks to another.
2.4.2 Draft and trim
The minimum draft for manoeuvring a tanker in SBT or CBT ballast is
mandated by IMO convention. Beyond that requirement there are other
considerations the master and chief officers must be aware of. Sufficient
propeller immersion is important to prevent cavitation erosion of the
propeller blade tips. Fair weather requires about one meter of immersion,
two meters for moderate weather, and three meters for heavy weather.
The forward draft should be sufficient to prevent the bow from slamming
or pounding in heavy seas, but not so deep that seas are taken over
the bow.
Trimming for speed is possible if the behaviour of the ship in ballast
has been carefully studied. Gains of 0.4 knots for the same fuel consumption
are possible through careful adjustment of the ballast trim. The optimum
trim for a 140,000 DWT ship is about four meters.
Trim and the ballast pattern together influence hull vibration. Vibration
increases hull fatigue and the incidence of cracking. A ballast plan
which reduces vibrations is preferred. To ensure that maximum time is
spent at best draft and trim, the tank washing and ballast changing
operations should be completed in the shortest time possible.
2.4.3 Motions
Placement of ballast within the hull affects the motions of the ship
at sea. The rolling period of the ship can be increased by placing ballast
outboard, in the wing tanks, structural strength permitting (see Section
2.4.1).
Pitching can be reduced by ballasting tanks near amidships, instead
of at the ends of the hull. This also helps to reduce 'pounding'.
2.4.4 Fuel consumption
Although heavy weather may be anticipated on a voyage, taking full heavy
weather ballast on departure will significantly increase fuel consumption.
It is preferable to take ballast for moderate weather and to divert
the vessel's course as recommended by a weather routing service. A weather
routed vessel normally arrives earlier, or not later than, one which
pursues the direct route. Weather routing produces less wear and tear,
and lower fuel consumption than the ship which slogs through the storm.
2.4.5 Corrosion
Intelligent ship owners ensure that the ballast tanks are protected
against corrosion by tank coatings and/or cathodic protection. Where
cathodic protection is carried the tanks must be filled completely for
the under-deck structure to receive the protective benefit of the anodes.
The best way to insure this is to open the tank lids after the vessel
is at sea, and fill the ballast tanks to overflowing. Do not do this
in port! It is better to fill the ballast tanks to a safe ullage in
port, and press them up to the vents or tanktops after departure.
2.4.6 Repairs/cleaning
If tank repairs, tank piping repairs, or tank cleaning are to be completed
during the ballast voyage, the ballast plan must be prepared to permit
washing and ventilation of the tank(s). When the cleaning is for entering
drydock, it may be necessary to clean both the CBT/SBT ballast tanks
and the cargo tanks.
2.4.7 Clean ballast
If cargo tanks will be washed for clean ballast during the voyage, the
vessel must depart with the selected tanks empty to permit early cleaning
after departure.
2.4.8 Ballast records
A comprehensive file of ballast plans should be maintained. The record
should indicate all weights in the ship (ballast, fuel, and water),
along with the drafts produced, and an indication of the speed and fuel
consumption achieved. The record is best maintained by computer files,
or in a bound journal with the facing pages being a ballast diagram
and a page of text and notes of the ballast voyage particulars. All
ballast handling details must also be recorded in the oil record book.
Exact times and positions of discharging ballast or decanting slops
should be recorded and may be invaluable if the ship is investigated
because of oil pollution caused by another vessel.
2.4.9 Efficiency
A good ballast plan achieves maximum efficiency by providing the best
trim to achieve the maximum speed during the voyage, and by structuring
the tank washing and ballast change operations to minimise washing and
ballast pumping time.
|