3.29 CARGO MEASUREMENT AND CALCULATION
The purpose of gauging ship tanks is to provide a verification of
the quantity said to have been loaded from the shore tanks and to determine
the quantity of water on board at the conclusion of loading. The quantity
of cargo used for the bill of lading is determined by shore tank measurements.
Normally, the shore tank measurements will be witnessed by an independent
petroleum inspector and perhaps by a loss control auditor employed by
the shipper. Occasionally, a representative of the cargo insurer is
also present. While it is obvious that the seller of the cargo would
benefit by exaggerating the quantity loaded from the shore tank, any
gross exaggeration is certain to be detected. The terminal's best chance
of regular gains on such transfers is simply to take advantage of those
measurements where the gauger is allowed to use his discretion. The
basic rule for shore terminal loadings or receipts, is to 'Maximize
the opening volume ... and minimise the closing volume.' This is done
at tank 'opening' gauges by choosing the next lower degree of temperature
and/or the next smaller ullage graduation whenever the observation falls
between graduation marks on the thermometer or gauging tape. When 'closing'
the shore tank after loading, the next higher degree of temperature
and/or next greater ullage graduation is chosen if the measurement offers
the opportunity to choose between readings. This practice applies regardless
of whether the tank is receiving or delivering oil. If it is applied
consistently, the terminal will produce a significant net gain of product
for the terminal owners over any period of time, without violating any
law or contract.
Numerous petroleum loss control studies have demonstrated that a large
portion of tanker cargo 'losses' in transit were never losses at all,
but rather inaccuracies in the measurement of shipping and receiving
shore tanks.
The volume of cargo in the ship's tanks is determined by measuring the
distance from the surface of the cargo to a datum point in the cargo
hatch or in a sounding pipe. This point is called the ullage point and
the distance is called the ullage, (see figure 3.29.6)
Making ullaging measurements is not difficult, but errors are frequently
made, therefore close attention and care are essential. Errors are normally
the combined result of three factors:
- Improper measuring technique.
- The use of non-standard or worn measuring equipment.
- Insufficient accuracy when ullaging and making temperature measurements.
There are many opportunities for inaccurate measurement on the tanker.
The ship is floating in a liquid and filled with a liquid, a condition
likely to produce motion of the cargo surface during measurement. The
tank hatch measurement area may be worn from years of service and the
datum point eroded. If the gauging tape is old, it may be elongated,
or the eye between bob and tape-end snap worn away so as to increase
their overall length. Measurements taken in bad weather or in darkness
by personnel who are tired will include
more errors that otherwise. Nevertheless, it is important that as many
inaccuracies as possible be eliminated from this procedure, so that
the ship's cargo measurement will correlate properly with the shore
figures and vessel's previous loading experience.
3.29.1 Checking equipment
Before gauging ship's tanks, all equipment should be checked for correct
performance and measurement accuracy. The ullage tape should be checked
with a steel rule to verify that the bob's point is the zero point of
the tape, or in some tape/bob combinations, that the zero mark on the
bob corresponds correctly to the zero point for the tape to which it
is attached. This check must be done for both manual and electronic
ullage tapes.
If cup case thermometers are to be used, they should be verified against
a standard thermometer and any with significant errors discarded. Minor
errors should be indicated as a correction to the thermometer reading.
To further reduce the effect of thermometer inaccuracies, each cup-case
thermometer should be designated/ dedicated to a specific tank. Using
the same thermometer in the same tank at loading and discharging ports
reduces apparent tank losses or gains. Even when new, it is possible
for standard cup-case thermometers to have errors of as much as 3 °C.
Calibration of thermometers is best done in a constant temperature water
bath, but placing all thermometers on a cloth on a table in an unventilated
room for ten minutes and checking them against a standard, certificated
thermometer is acceptable.
Electronic thermometers are preferable to cup thermometers with respect
to both absolute accuracy and the accuracy with which the average temperature
in a tank can be measured. The probe can be lowered accurately to a
number of desired depths and a series of stabilised measurements made
each 20 seconds. Some types have automatic averaging calculators and
will indicate the average temperature of the tank on command.
Electronic temperature sensors in ullaging units may also be checked
on board by comparison with a certified thermometer, however all portable
electronic temperature sensors should be standardised annually over
their complete working range (under laboratory conditions) and the calibration
noted on a calibration decal attached to the unit.
Automatic ullage tapes which give an audible signal for cargo surface
and cargo/water interface measurement should be tested before each use
by immersing in a clear container of oil and water and confirming that
the correct sound tones are produced at the correct levels.
Necessary lights for night gauging, personal protective equipment, breathing
apparatus (if necessary), hydrocarbon vapour test equipment and the
necessary forms for recording the measurements should all be ready in
advance of taking ullage readings.
3.29.2 Confirming draft, trim and list
Prior to any cargo ullages being measured, the draft should be accurately
read all around the ship and the trim and list also determined and agreed
by all parties.
More cargo measurement errors at the loadport are caused by failing
to determine and apply trim/list corrections than any other reason.
This failure could expose the ship to unexplained, or 'apparent' transit
losses, (or gains), at the discharge port.
The completion of the loading operation is usually a hectic time for
the crew, as pressure is placed on the ship to sail as soon as possible.
Nevertheless, the chief officer should not be persuaded to commence
any cargo ullaging until all operations that might affect the trim or
list of the vessel have been completed.
The position of each gauging point in relation to the tank will have
an important bearing on the accuracy of cargo measurements. On only
a few vessels will the gauging point be in the 'centre' of the tank
where it is unaffected by trim or list.
The most accurate measurements will be when the vessel is on an even
keel with no list. Any deviation from this condition will require corrections
to the tank calibration table quantities. Such corrections are variable
in their accuracy and are the least accurate when the cargo surface
is not contained in a 'box' shaped tank. Forward wing tanks and the
upper hopper spaces of OBO vessels are particularly prone to error in
their list or trim corrections.
On many newer vessels, the traditional wing cargo tanks have been replaced
by protectively located segregated ballast tanks (PL-SBT), leaving only
the centre tanks for cargo. These centre tanks are often wider than
they are long. Corrections to list are particularly important in such
tanks.
Example
A 1991 built 135,000 DWT crude tanker has all the official gauge points
sited aft and to the port side of each tank. The trim and heel correction
for one of these tanks is as follows:
Tank No.4 °C
1.0 m. aft= 4.5 cm ullage correction.
1 deg. list = 27.0 cm ullage correction.
Consider a mere 1/10 degree list which would be essentially undetectable
by the average clinometer and the list correction will still be 2.7
cm.
On this vessel, with 7 main cargo tanks, each with 1 cm. of ullage =
63 barrels, the 'error' in measured quantity from failing to detect
and correct for a 1/10 degree list is 1190 barrels.
When correcting for trim and list, it is imperative that any free water
found also be corrected. For small amounts this may require correction
by use of the wedge formula.
3.29.3 Measuring cargo ullage
Tanks containing static accumulator oils should not be sampled or ullaged
until thirty minutes after they have stopped receiving cargo. However,
gauging can begin with the first set of tanks loaded, and finish by
measuring the trim tanks last.
On non-inerted ships, or inerted ships where IGS pressure has been reduced
for gauging and sampling, only one tank at a time should be opened.
Gauging should be completed first, followed by sampling. Synthetic lines
should never be used for lowering sampling containers or thermometers;
use cotton line for this.
Steel tapes should be earthed to the tank hatch before the bob is placed
in a tank containing static accumulator oil.
Measurement readings should be made by the independent inspector and
recorded by a ship's officer.
On inerted ships, or where electronic, closed gauging equipment is used
the following procedures should be followed:
- Lower the probe carefully into the tank by slowly unwinding the tape.
The probe must not be allowed to descend under its own weight (as with
steel tapes).
- When the audible signal indicates that the probe has reached the liquid
level it should be withdrawn slightly and then lowered again, noting
the exact reading when the audible signal is first heard.
- Repeat withdrawing and lowering the probe until three readings are
obtained which all agree within 5 mm.
Each tank measurement must be witnessed by a ship's officer and a
terminal representative. The ship's officer should record the readings
for the independent inspector and the terminal representative should
make a second copy as the reading is told off. Later the two sets of
readings will be compared and any tank for which two records do not
agree must be re-measured.
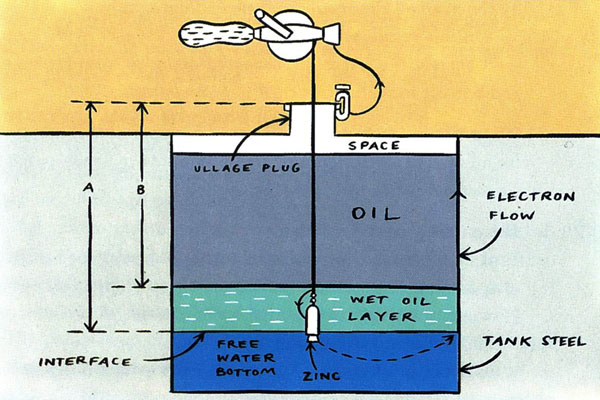
Oil/water interface detector.
The ship's officer should have with him (in his deck notebook), a
list of the total gauge depth of each cargo tank. This is used to verify
that the tape is lowered to tank bottom and no further, when taking
the water measurements. Tanks must be 'thieved' for water, either by
use of an electronic sensor, or by coating the bob of the ullage tape
with litmus paste and lowering it to the tank bottom. When it is retrieved,
the height to which the coated bob has changed colour is the measurement
of the level of water depth at the bottom of the cargo. If the bob is
allowed to fall over and lie flat on the bottom, then one inch of water
in the bottom of the tank would appear to be six inches when the bob
is retrieved. And if it is not lowered completely to the bottom, then
water received from the shore terminal may not be detected by the ship
tank gauges. The officer's job is to see that the measurement is made
correctly. A crew member should be assigned to follow behind the sampling
crew to clean and secure each sampling opening after the tank has been
gauged and sampled.
The slop tank(s) should be measured last. Determination of the oil/water
interface is made much easier if an electronic probe unit is used. Measurements
of temperature must be for the oil level only. Do not take temperature
measurements of the water layer.
The independent inspector should complete his cargo measurement observations
by verifying and recording the seal numbers on any cargo valves which
were sealed before loading. He should also verify that the numbered
seals placed on sea suctions before loading remain intact when loading
is completed.
If the ship is fitted with automatic tape or electronic (radar), tank
ullaging equipment of sufficient accuracy, the ullages should be taken
with the fixed units. The tapes or sounding devices must be in good
condition and their calibration records available for review by the
petroleum inspectors. If both manual gauges and automatic gauges are
taken and recorded, the chief officer should later use the ullage records
to determine the accuracy of his automatic gauges.
3.29.4 Ullage measurements at sea berths
If the vessel is exposed to swell or other conditions affecting the
measurements (such as high winds while open gauging), an ullage based
on the average of three measurements may be used in lieu of three consecutive
measurements within 5 mm.
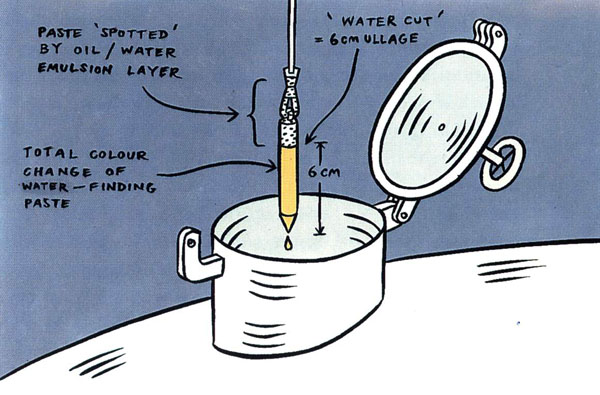
Typical 'cut' on paste-coated bob.
When exposed to swell in a sea berth, waves will form in the cargo
causing an apparent reduction in the measured ullage as the wave crests
traverse the ullaging point. The most correct reading(s) will be those
taken when the vessel's roll amplitude is at a minimum. Ullages taken
in sea berths normally overstate the amount of cargo in the ship. The
weather and sea conditions at the time of measurement should be carefully
noted on the ullage record and in the logbook.
3.29.5 Temperature measurements
Temperature measurements should be made with procedures and equipment
conforming as closely as possible to the recommendations of the American
Society for Testing and Materials (ASTM) and the American Petroleum
Institute (API). Errors in cargo tank temperature measurement of 1 °C
can produce calculated volume errors of 0.1% for crude oils of average
density and 0.2% for light products and light crudes.
Use of only a single thermometer lowered to the centre point of the
cargo should be avoided. Cargo tanks may have a temperature difference
of 5 °C between top and bottom. If cup-case, mercury thermometers are
used, temperatures should be observed at three or more levels in the
tank.
The preferred method is the modern thermal probe with digital output
(usually combined with the ullage tape). Using a digital probe permits
temperature measurement intervals as small as one meter. Some probe
units sound a tone when the temperature reading has stabilised and the
reading can then be recorded in memory (by pushing a button). If this
feature is not included, then the probe must be held at each level for
20 seconds before recording the measurement.
ASTM D1086 (heated cargo) guidelines suggest that cargo tanks with more
than 4.5 meters of liquid depth require three temperature measurements,
one each at 1 meter from top and bottom and one at
the middle.
Another standard, Institute of Petroleum IP 204/86 recommends temperature
measurements at 1/6, 3/6, and 5/6 of cargo innage depth. If the temperature
of the middle sample is within 1 °C of the average of the three temperatures,
the average may be used. If the middle temperature is outside the one
degree tolerance, then additional temperature measurements should be
made at 9/10, 7/10, 3/10 and 1/10 of cargo depth and the average of
all seven used, provided the middle temperature is within one degree
of the average. If not, more temperature observations are recommended
(but in practical application are rarely taken).
3.29.6 Calculating cargo quantity
When the cargo density at 15 °C (or the API gravity at 60 °F, if using
Imperial units), all tank ullages, average cargo temperatures (by tank)
and water innages have been recorded, the calculations of cargo volumes
loaded can be completed. This will be done manually by the independent
inspector, but may also be done with the aid of the ship's loading/stability
computer.
Each tanker has a set of certified calibration tables for the cargo
and slop tanks. The tables indicate the amount of cargo in each cargo
tank for ullages at one centimetre (or inch), intervals. Volumes for
ullage readings between even centimetres (or inches), are determined
by linear interpolation or by referring to a millimetre (or fractions
of an inch) table for the tank. After the observed volumes are determined,
the rest of the calculation follows.
Pipelines
Allowance should also be made for pipeline or duct keel volumes to be
included in the calculations if they are not included in the calibration
tables. For pipelines which run through the cargo tanks, the average
temperature of the cargo in all tanks will suffice for the correction
factor of cargo in the pipelines. For pipelines external to the cargo
tanks, the average cargo temperature may be used at the loadport. At
the discharge port, the average cargo temperature may still be used,
or the volume may be assumed to be at standard temperature (ie. 60 °F
or 15 °C). The difference will be minimal.
Example
Consider a vessel with duct keel of volume 1000 barrels filled with
crude oil of 30.0 ° API gravity after loading then:
1000 bbls. @ 60 °F = 1000.0 bbls.
1000 bbls. @ 50 °F = 1004.4 bbls.
1000 bbls. @ 70 °F = 995.5 bbls.
The 'error' involved for each 10 °F difference in pipeline cargo temperature
is insignificant.
Units of measurement
Different countries will normally utilise metric or imperial units as
follows:
Metric (cubic meters):
TOV - Free water = GOV x vcf (tables 54A/54B) = GSV @ 15 °C (cubic meters).
Imperial (barrels):
TOV - Free Water = GOV x vcf (tables 6A/6B) = GSV @ 60 °F (barrels).
Total observed volume (TOV)
Total observed volume is the total measured volume of all petroleum
liquids, including sediment and water (S&W) and free water, measured
at the observed temperature and pressure. It is determined by converting
the observed ullage readings to volumes using the vessel's tank calibration
tables and adjusting the volumes with the necessary trim and list corrections.
This is for designated cargo tanks only. The slop tanks may or may not
be included, but this must be clearly indicated in the report.
Gross observed volume (GOV)
Gross observed volume is the total measured volume of all petroleum
liquids, including S&W, but excluding free water, at observed
temperature and pressure.
Net observed volume (NOV)
Net observed volume is the total measured volume of all petroleum liquids
excluding S&W and free water, at the observed temperature
and pressure. S&W can be estimated by centrifuge, but standard petroleum
sale contracts call for S&W measurement by filtration and chemical
titration respectively.
Gross standard volume (GSV)
Gross standard volume is the total measured volume of all petroleum
liquids and S&W, but excluding free water and corrected
by the appropriate temperature correction factor for the observed temperature
and API gravity (or density), to a standard temperature, 60 °F. (or
15 °C.) and also corrected by the applicable atmospheric pressure correction
factor.
Net standard volume (NSV)
Net standard volume is the measured volume of all petroleum liquids
excluding S&W and free water and corrected by the appropriate
temperature correction factor for the observed temperature and API gravity
(or density), to a standard temperature such as 60 °F (or 15 °C and
also corrected by the applicable pressure correction factor.
The NSV is the commercially important result of the calculation process,
since it is the basis on which the cost of the cargo of oil is determined.
Total calculated volume
Total calculated volume is the GSV plus any free water measured
at the observed temperature and pressure.
The TCV is important to the chief officer because it will be the reference
quantity against which transit differences will be measured at the discharge
port. Since the vessel has no control over the amount of water contained
in the cargo, such water will often settle out during the voyage, resulting
in a much higher free water quantity at the discharge port than at the
loading port. Since free water is not corrected for temperature, this
quantity has to be added back to the GSV in order to accurately compare
the TCV 'after loading' to the TCV 'before discharge';
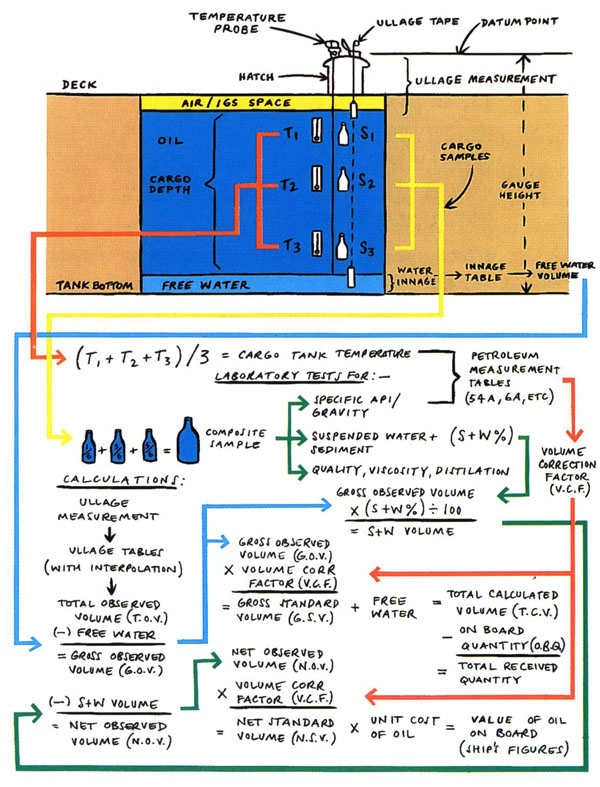
Diagram of the process of a cargo quantity calculation.
Total received volume or total delivered volume
The total received/delivered volume is the TCV less any OBQ/ROB found
in the designated cargo tanks after discharge is completed. This is
the quantity against which the vessel experience factor is applied to
determine the accuracy of the bill of lading.
In some countries, the density of the cargo used in these calculations
is determined in the laboratory in an artificial vacuum. This method
removes the factor of atmospheric pressure from the cargo calculation
process, but has two results:
- Quantities determined from densities determined 'in vacuum' (or 'in
vacuuo') are greater than the result obtained by the standard method
indicated above, and
- The method is not used in most countries and will conflict with the
quantities determined on arrival at the discharge port by the normal
density measurement method. Comparing the two figures without adjustment
or explanation will indicate an apparent (but false), in-transit cargo
loss.
In 1980 the petroleum measurement tables were updated with tables
6A and 6B replacing the old table 6. Several countries, including many
OPEC members, still use the old table 6 to calculate the bill of lading.
The effect of this is to overstate the bill of lading quantity and create
an erroneous ship to shore difference.
Calculation of the ship's cargo quantities should be done by individual
cargo tank. Calculating cargo by using the total tank volumes and average
temperatures and densities will produce a less accurate result due to
the different quantities in each cargo tank.
3.29.7 Comparison with shore figures
The master should issue a 'Letter of Discrepancy' for any and all ship
to shore differences as well as any free water found on the vessel after
loading.
The vessel experience factor (VEF) is used to compare ship and shore
figures. Before an accurate ship to shore comparison can be made, the
vessel's VEF must be determined. It is important to be aware of just
how accurate the VEF is for each individual ship. For example, if the
ship frequently loads above and below shore quantities, the resultant
factor may be close to 1.0000 and will not be accurate. The method used
to determine a vessel's VEF is frequently under review by the API, but
currently is as follows:
The VEF is a compilation of the history of the TCV vessel measurements,
adjusted for OBQ or ROB, compared with the TCV of shore measurements.
Separate VEF's should be developed for both the load and discharge operations.
Information used to calculate the VEF should preferably be based on
documents that follow accepted industry standards and practices, such
as inspection company reports.
Whenever possible, manual vessel measurements should be used for volume
determinations. Automatic gauging systems with accuracy/measurement
tolerance equal to or better than those of manual measurements may be
used for custody transfer by mutual agreement between all interested
parties. All calculation procedures, such as those for temperature,
volume correction factor, ROB/OBQ, wedge or trim factor, must be consistent.
Do not use long or metric tons. Quantities shall be expressed in either
barrels or cubic meters at standard temperatures, but shall not be combined.
Information from all load or discharge terminals should be used to calculate
the respective VEF's. If the information is available, the VEF can be
based on the data from the same load or discharge terminal.
Only voyages that qualify should be used in the compilation of a VEF.
A minimum of five qualifying voyages is needed to calculate a VEF, however,
a larger number is desirable. The definition of a qualifying voyage
is one that meets the following criteria:
1 Any voyage that is within +/- 0.0030 of the average
ratio of all voyages listed. (As an example, if the average is all voyages
listed is 1.00105, all voyages within the range from 0.99805 through
1.00405 would qualify).
2 Excludes all voyages prior to any structural modification
which affected the vessel's cargo capacity.
3 Excludes load or discharge data where shore measurements
were not available.
4 Excludes all voyages involving ship-to-ship lightering.
5 Excludes the first voyage after dry docking.
6 Excludes all voyages after non-liquid cargoes.
The VEF should be calculated to five decimal places.
When the shore loading figures and the result of the ship's cargo calculations
are available, they should be closely compared. There should be close
agreement between the ship figures divided by the VEF and the shore
figure. If the ratio of ship/shore falls outside the range of the previous
experience or is greater then permitted by the charter party, then a
close examination of both shore and ship cargo gauges and calculations
must be made. If the source of the discrepancy cannot be determined
(and corrected), the master must deliver a letter of protest to the
shippers' representative against the difference The presence of water
in the cargo is also cause for a master's letter of protest, including
a note that 'free water may increase during the voyage'.
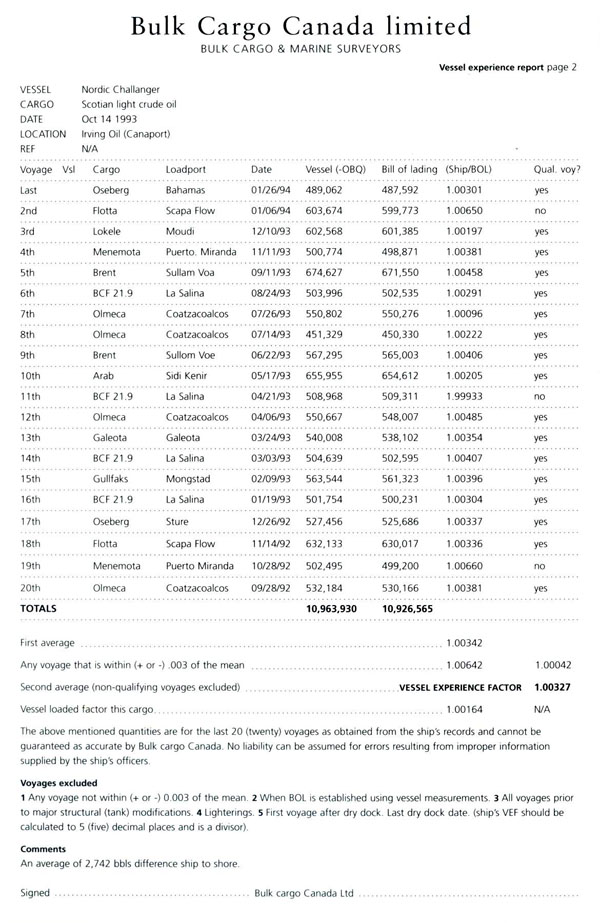
Example of vessel experience report.
The vessel cargo temperatures should be checked against the shore
tank temperatures. If there is a difference of more than 2 °C the following
actions should be taken:
- If the vessel cargo temperature is higher than the shore, then:
• Give a protest letter to the shore terminal, and
• Enter the temperature difference on the vessel's cargo papers.
- If the vessel's temperature is lower than the shore, then:
• Enter the temperature difference in the vessel's records, and
• If the temperature difference is more than 4 °C, request the shore
terminal to check the accuracy of the shore temperature measurements.
If no error is found or correction made, submit a protest letter to
the terminal.
3.29.8 Cargo quantity report
When the cargo figures have been agreed, the petroleum inspector will
prepare a report which he will ask the master and/or chief officer to
sign. This appropriate officer should sign the report, indicating 'For
ullages and temperatures only' and 'protest noted' if one has been made.
The ship will have a corresponding owner's/charterer's document which
the independent inspector will be asked to sign. He may refuse to do
so, as most will not sign any but their own documents. In any event,
the vessel's records of cargo loaded must include the printed names
of the independent inspector (along with his company's name), the name
of the officer witnessing the cargo measurements and the name of the
chief officer.
|