3.6 CONNECTING CARGO HOSES/LOADING ARMS
The connection of cargo hoses or loading arms is an industrial operation
requiring a number of prior inspections and precautions. A large percentage
of personnel injuries on tankers occur while cargo hoses are being connected.
If a work permit system is in use on the tanker, a work permit should
be completed for the cargo hose connection operation.
3.6.1 Inspection
The following inspection items must be completed prior to connecting
hoses or arms:
If ship's derricks are to be used, inspect:
Topping and cargo runner winches.
Topping lift wires and runner wires for condition.
Chains and shackles.
Deck and kingpost fittings and welds for cracks or corrosion.
Guys or running rigging for condition/damage.
Lubrication of all lubrication points.
Determine the weight of the hose string and compare it to the derrick/crane
lifting capacity.
Crew personal protective equipment: hard hats, shoes, gloves, eye protection.
Portable fire extinguishers.
Connection tools, studs, nuts and gaskets.
Hose stoppers, slings, or bridles.
Inspect the condition of all manifolds to be used, clean/dress any
soiled or corroded flange faces.
Provide new gaskets for each manifold to be used.
Hose flange studs and nuts previously used in one discharge
port may be re-used for one loading port, but should be
discarded thereafter.
Oil adsorbent, brooms, scoops and trash containers.
Fire hoses connected and ready.
Prepare the hose manifold containment trough and trough pumping-out equipment.
Label the manifolds to be used for loading cargo. If multiple grades
of cargo will be loaded, label both sides of each manifold valve with
the name/grade of cargo to be loaded. As each hose or arm is brought
aboard determine the grade of material to be loaded through that arm/hose
and mark it with chalk on the surface of the arm/hose.
The chief officer should also examine the condition of the shore terminal
hoses, derricks, loading arms, connecting flanges, gaskets, connecting
devices, supporting equipment and personnel protective equipment and
to tactfully point out any defects. Hoses should be inspected for kinking,
crushing, chaffage, cuts and breaks. Equipment, especially hoses, showing
any significant defect should be refused for purposes of loading the
cargo. After cargo loading begins, check for sweating, pinhole leaks,
bulges, or any leaks around the hose carcass to metal flange joint.
The derrick must be properly positioned ('spotted') to minimise hose
handling. Use light tackles or come-alongs to aid hose positioning efforts.
Hoses should be fully supported during connection. The hose connection
operation provides numerous opportunities for crushed/ broken hands
or fingers if conducted carelessly. Ensure that only competent personnel
operate winches and that they fully understand any hand or verbal signals/orders
to be used.
3.6.2 Shore bonding wire
Studies have indicated that a ship-to-shore bonding wire does not achieve
the purpose for which it was intended unless the wire is an impracticably
large diameter. The preferred method of preventing incentive sparks
when the shore arm/hose is brought in close proximity to the ship's
manifold is to have installed an insulating hose length or insulating
flange connection in the shore hose/arm. The insulating flange prevents
the passage of any current from one structure to the other and eliminates
the possibility of an incentive sparks, as long as the insulating gasket
is properly maintained! On each side of the insulating flange or hose
length, the arm or hose must be electrically continuous to the ship
or dock to dissipate any static electric charge produced by the moving
oil.
Nevertheless, the use of bonding wires continues to be mandated at some
terminals. If required it should be connected as follows:
Verify that the bonding wire switch is in the open position.
Find an exposed metal point away from the loading manifold and connect
the bonding wire clamp to it.
Close the bonding wire switch.
Connect the loading hoses/arms.
3.6.3 Connecting hoses/arms
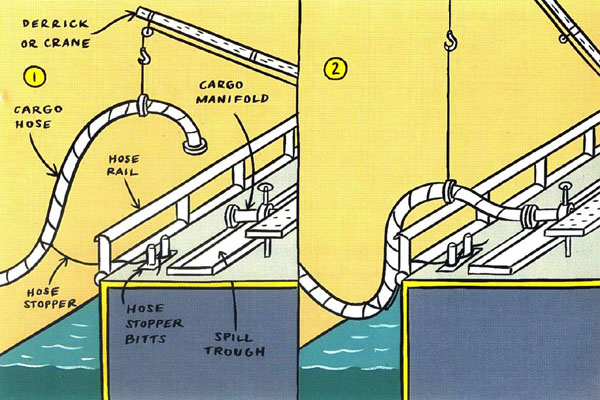
By properly positioning the hose stopper, the
connection operation becomes safer and easier.
1 The hose is lifted high overside
and the hose stopper is passed around it and made fast on deck. 2
As the hose is lowered the stopper takes up most of its weight making
it easier to manoeuvre the hose into position for connection.
Where the dock is located well below the ship's hose rail, the hose
must be hoisted well up, then a stopper made up on the hose stopper
bitts to control the level of the hose while it is connected. A reliable
seaman must be put in charge of handling the hose stopper.
After the connection is made, check that the hose support rigging is
suitably positioned for the entire duration of the loading.
Loading arms are normally connected by the shore terminal personnel,
since they are operated by hydraulic equipment located on shore. The
ship's officer in charge should conduct the inspections indicated above
and observe the connection operation carefully to see that it is properly
completed.
Shore hoses or arms should be empty when brought aboard. If the hoses
or arms are full they must be drained into the ship's manifold trough
before connecting. Shore personnel must agree to let the ship pump the
drainings to the shore containment. After the arms have been connected
verify that the loading arm support stand is properly set and tightened
up. Also verify that the loading arm vent is closed. Make a logbook
entry for the time each hose/arm is connected and the manifold to which
it is connected.
|