2.2 CLEAN BALLAST TANK SYSTEMS AND PROCEDURES
Tank ships which are not equipped with segregated ballast tanks (SBT)
may use their cargo system piping to take ballast into tanks reserved
from carrying cargo. These reserved, clean, ballast tanks (CBT), are
either original cargo tanks set aside for this purpose, or specially
constructed tanks. The original purpose of the CBT concept was to provide
an interim step between the earlier system of placing ballast in cargo
tanks, and the ultimate goal of requiring SBT for all tankers. CBT was
intended to reduce creation of oil and water mixtures on ships which:
Are not provided with SBT, or
Cannot COW because they do not carry crude oil.
Some CBT tankers have a pump and line sections reserved for ballast. The
ballast operation for these ships are a combination of CBT and SBT procedures.
The CBT filling and discharge procedures involve several opportunities
for a pollution incident if they are not conducted exactly according to
approved procedures.
Case history
In late 1990 a 57,000 DWT product/crude carrier arrived in Boston to off-load
cargo. On arrival the ship requested a United States Coast Guard tank
vessel examination letter. The previous letter has been withdrawn after
a Coast Guard examination at Philadelphia revealed several deficiencies.
That action was followed by two oil spills, after which the ship's crew
was changed.
In Boston five of the vessel's seven ballast tanks were found contaminated
with oil. In addition, ballast was being carried in a centre tank, contrary
to the IOPP certificate which listed the corresponding wing tanks for
CBT. The ship's chief engineer confessed that he had pumped engine room
bilges into the same centre tank. Further inspections revealed undocumented
changes to the ballast system and inoperative ballast valves. Other ship
systems were found in a similar state of disarray and disrepair.
The vessel was denied entry into the port of Boston. The classifications
society withdrew the ship's IOPP and SOLAS certificates. Local news media
featured the vessel and its owners and operators on the evening news.
The US Coast Guard began assessment of civil penalties for violations
of MARPOL ANNEX I. The ship was issued a temporary certificate to depart
on a one-way voyage to off-load its cargo, and then proceed directly to
shipyard.
Case analysis
To say that the condition of this ship in the above case demonstrates
deplorable management would be an understatement. Like the worst absentee
landlords, the owners had obviously let the vessel deteriorate until it
was a hazard to its crew and to the environment. It is possible that the
vessel was being managed under a technical management contract instead
of directly by the owner. Such an arrangement would not excuse the owner
from his obligation to know the condition of his ship and correct significant
defects.
The most difficult position in this case is that of the master and crew.
They find themselves employed on a sub-standard ship, in a foreign port,
caught between clear and specific rules and requirements and an owner
who refuses to provide the means for compliance. What should they do?
The only thing to do in a case like this is to proceed as far as the condition
of the vessel permits, then stop and advise the owner that operations
cannot proceed because of the defects or conditions noted. The worst the
owner can do is replace the crew. In this case, the vessel's officer's
attempted to proceed with the defects unrepaired. For their efforts, they
will have personal records in the US Coast Guard computer files, they
will be reported to the authority which issued their licenses, and they
were replaced!
Something every ship's officer should understand is that no owner will
support him if he has broken the law. Some officers bend or break pollution
regulations because they think the savings of time or cost will be appreciated
by the owner. In truth, any good owner would be appaled by such actions.
The fines and penalties to which the owner may be exposed by the infractions
of some well-meaning crew member far outweigh any possible saving. Conscientious
owners expect that their crews will follow both laws and company policies
with equal diligence as the best way of safeguarding the owner's interests.
2.2.1 Clean ballast systems
The requirements for CBT systems and CBT operations are detailed and
specific. They are set forth in IMO Resolution A.495 (XII) of 1981.
Unlike segregated ballast tank (SBT), systems, clean ballast tank ships
do not have complete separation of the ballast and cargo systems. A
CBT ship uses some of its cargo piping, pumps, and valves to load and
discharge ballast from the clean ballast tanks. However, it has become
an apparently permanent fixture of older tankers, giving them an extended
economic life and continued opportunities to cause operational pollution.
The CBT system has added complexity to existing tanker operations. Using
it properly requires careful study of the particular system, close attention
to the procedures for conducting each step of CBT operation, and time.
The most difficult CBT operation is ballasting at the discharge port.
2.2.2 CBT operations in the discharge port
All CBT operations begin by flushing cargo pipelines with water from
the clean ballast tanks. In the discharge port, where the ship arrived
full of cargo, the CBT tanks must either contain retained ballast for
flushing, or flushing water must be added 'over the top' while the ship
is discharging. If adequate ballast for flushing was not retained when
departing the loading port, it may be added in the discharge port using
the ship's fire main system, bilge and ballast system, or through some
other means. The ballast tanks must contain an amount equal to either
ten times the volume of the piping they are required to flush, or enough
ballast water to prevent vortexing until the piping has been run full
of water. This amount will be specified in the ship's CBT manual.
2.2.3 CBT manual
Each tank vessel which operates in the CBT mode is required to have
a CBT operations manual specifically prepared for it. The required content
and format of this manual is prescribed in the IMO publication Dedicated
clean ballast tanks, revised specifications for oil tankers with dedicated
clean ballast tanks and standard format for the dedicated clean ballast
tank operation manual. An example CBT operation manual and diagram
are included in the IMO booklet. Despite the IMO efforts to provide
clear direction for CBT operations, many vessels do not conduct their
CBT operations properly.
The IMO guidelines should be recognised as the minimum written procedures
an operator should provide to insure correct ballast operations. It
is recommended therefore that managements should take care to prepare
scrupulously detailed and illustrated instructions for each CBT operation.
The instructions should include the following:
Presentation of the CBT operations by type, ie:
Loading port operations.
Extra or heavy weather ballast.
Discharge port operations.
Other operations. Identification of all CBT valves by number.
Presentation of CBT operations in single steps.
Illustration of each step with a colour-coded line diagram.
Checklists for each CBT operation.
Instructions for sealing, lashing, or locking critical valves
which must remain closed.
The following is an example CBT operation at the discharge port. The
system plan and valve numbering is the same as contained in the IMO
Dedicated clean ballast tanks guide (1982 edition, reprinted
1987). The instructions have been presented in a step by step fashion,
with illustration for each.
It is assumed that the clean ballast tanks contain sufficient water
to perform the preparatory flushing operations described. If sufficient
flushing water is not in the tanks at the start of the discharge, it
must be transferred to them using the ship's fire main and hoses, or
by some other means.
Readers will note in some places that the instructions call for the
crew to 'close all valves', and then instruct that a valve just closed
is to be opened again. This is intentional. Few tanker contaminations
or pollution incidents have ever been caused by a valve improperly left
closed. Pollution and contaminations are caused by valves incorrectly
left open! Any valve not in immediate use should always be in a closed
position. Where a complex transfer operation is to be conducted, especially
as in the case of flushing pipelines, the only sure way to properly
set the valves is to close all of the valves in the system, then open
those required for the next step.
CBT operations after cargo discharge is complete:
-
Complete the discharge of all cargo from the ship's tanks. Strip
pumproom risers and deck discharge lines ashore:
- Thoroughly strip the No.l and No.2 pumproom cargo risers and the
deck discharge lines into the No.3 cargo line and ashore via the No.3
port manifold. (This step is essential to preventing harbour pollution
when the sea chest valve is opened to provide ballast water.)
The following steps are required:
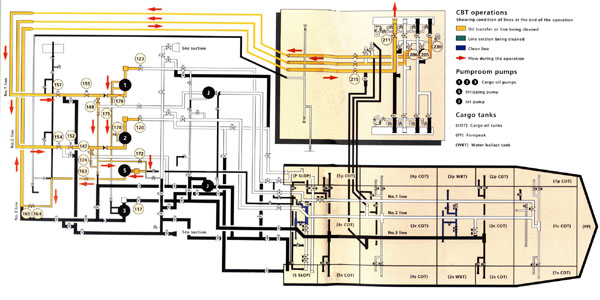
1 Open valves:
148 (No.1 pump discharge to jet pump), 175 (stripping
suction to No.1 line), 179 (No.1 cargo pump stripping suction), 172
(stripping pump suction), 147 (No.2 pump discharge to jet pump), 174
(stripping pump suction to No.2 line), 178 (No.2 cargo pump stripping
suction), 163 (stripping pump discharge valve), 164, 165 (stripping
discharge to No.3 line),
205 (No.1 line manifold vent valve),
206 (No.2 line manifold vent valve), 230 (manifold vents inlet valve),
(Valves 152, 154, 155, 157, 215 and 211 remain open from cargo discharge.)
2 Close cargo pump suction valves 117, 120 and 123.
3 Start the stripping pump. Continue
to strip lines until pump loses suction.
4 Close valve 172.

Strip No. 1 bottom line ashore:
5 Open valves:
162 (stripping suction to pumproom suction crossover
line),
122 (sea suction crossover block valve),
124 (No.1 pump suction crossover valve),
144 (No.1 line pumproom block valve),
104 (No.1 line pumproom bulkhead valve),
60, 59 (No.1 line block valves).
6 Start stripping pump.
When stripping pump has developed a suction vacuum
on No.l line, open valve 24 (No.1 centre tank main suction valve). The
vacuum in the line will drain the length of the No.l line and the No.1
deck drop without allowing any cargo to fall back into the tank.
7 When stripping pump loses suction,
stop the pump.
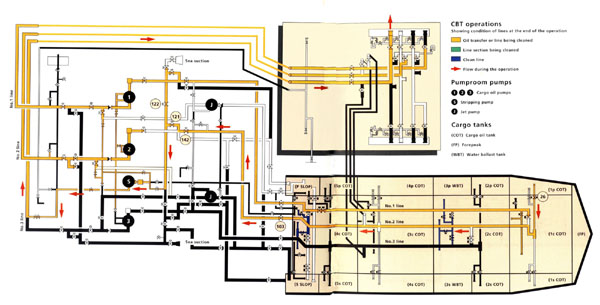
Strip No.2 bottom line ashore:
8 Close valve 122.
9 Open valves:
121 (pumproom crossover to No.2 cargo pump suction),
142 (No.2 cargo pump block valve),
103 (No.2 line pumproom bulkhead valve).
10 Start stripping pump.
When a vacuum is indicated on No.2 line open valve:
26 (No.1 port cargo tank main suction valve).
11 When the stripping pump loses
suction, stop the pump.
12 Close valve 26.
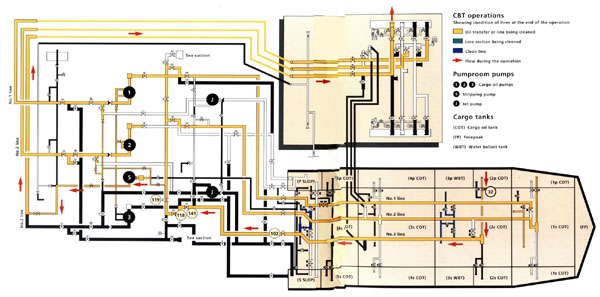
Strip No.3 bottom line ashore:
13 Open valves:
119 (sea suction crossover block valve),
118 (pumproom suction crossover to No.3 line),
141 (No.3 pump suction block valve),
102 (No.3 line pumproom bulkhead valve).
14 Start the stripping pump.
When a vacuum is indicated on the No.3 line open
valve: 32 (No.2 port cargo tank main suction valve).
15 When stripping suction is lost,
stop the pump.
16 Close all valves.
3. Strip the No.3 pumproom riser and deck line to the
starboard slop tank:
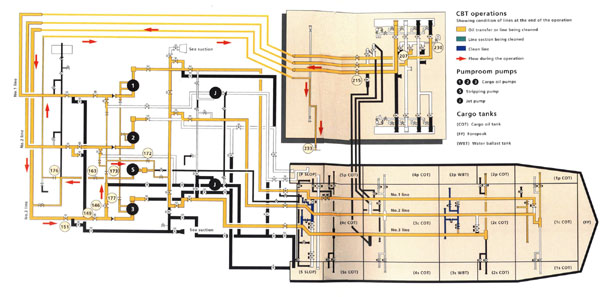
1 Open valves: 173
(No.3 to jet pump supply line stripper suction),
172 (stripping pump suction valve), 163 (stripping pump discharge valve),
176 (stripping pumproom riser valve), 233 (drop valve to starboard slop
tank),
146 (No.3 pump discharge to No.3 jet pump valve),
177 (No.3 cargo pump stripping suction), 149 (No.3 pump discharge valve),
151 (No.3 line pumproom riser), 215 (No.3 deck line block valve), 207
(No.3 line manifold vent valve), 230 (manifold vents inlet valve).
2 Start stripping pump. When
pump loses suction, stop stripping and close all valves.
All residual cargo has now been removed from the ship's pipelines. The
next step prepares the lines for receiving clean ballast by flushing them
with retained ballast water from the CBT tanks. 4.
Prime the No.l cargo pump
1 Open valves:
123 (No.1 pump suction valve),
144 (No.1 line pumproom block valve),
104 (No.1 line pumproom bulkhead valve),
60, 59 (No.1 line, block valves),
41, 40 (No.l to No.3 lines crossover block valves),
36 (No.2 centre rank stripping suction valve).
2 After one minute: close
valve 36 (No.2 centre stripping suction), open valve 37 (No.2 centre
tank main suction valve).
3 Wait thirty minutes
(to allow the water to remove oil clingage from
the pipeline walls).
4 Vent pump casing to insure
pump is primed.
5. Flush No.3 centre tank branch line and
No.1 main cargo line to port slop tank from No.2 centre tank:
1 Open valves:
148 (supply to No.1 jet pump), 160 (No.1 jet pump
block valve), 110 (No.1 jet pump bulkhead valve), 133 (port slop tank
fill valve).
2 Start No.1 pump and flush from
No.2 centre tank main suction, via No.1 line, and discharging through
the No.1 jet pump to the port slop tank.
3 Flush for three minutes.
4 Stop the No.1 pump.
5 Close valves:
37 (No.2 centre tank main suction valve), 40,
41 (No.1 line to No.3 line crossover), 59, 60 (No.1 line, block valves).
6. Flush the No.1 pumproom riser, deck line, and
deck drop line from No.4 centre (ballast tank) to the starboard slop tank
via No.2 line:
1 Valves 104, 144, 123 remain open
from the previous operation.
2 Open valves:
67 (No.4 centre ballast tank main suction valve),
58 (No.l line to No.4 centre tank suction block),
155 (No.1 pump discharge valve),
157 (No.1 line pumproom riser valve),
217 (No.1 line deck block valve},
214 (No.1 line deck drop valve),
25 (No.1 line to No.2 line crossover valve),
103 (No.2 line pumproom bulkhead valve),
142 (No.1 pump suction block valve),
143 (No.2 line crossover valve to port slop tank suction/fill line),
111 (port slop tank suction/fill valve).
(Note: valves 40, 41, 36, 37, 59, 60 and 156 are closed for this operation.)
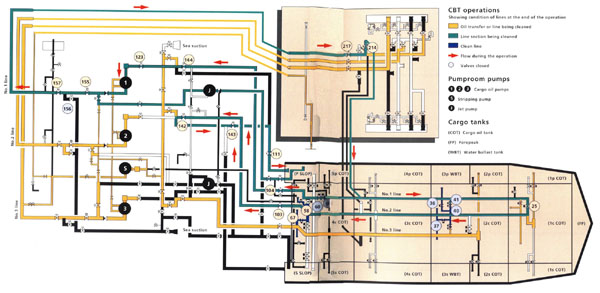
3 Start No.1 pump and flush at
slow speed for thirty minutes from No.4 centre ballast tank, via pumproom
risers, deck line, deck drop, No.2 line and pumproom into port slop
tank.
4 Stop No.1 pump.
5 Close valves:
104 (No.1 line pumproom bulkhead valve), 144 (No.1
pump suction block valve).
7. Flush the ballasting line (No. 1 line) to the port slop tank from
the sea:
1 Open valves:
125 (port sea suction block valve),
124 (No.1 line to pumproom crossover valve).
2 Start No.1 pump.
3 Open valve 126 (port sea suction).
4 Flush from sea via pumproom
riser, deck line, deck drop No.l and No.2 bottom lines to port slop
tank.
5 Stop the No.1 pump.
6 Close valves:
25 (No.1 line to No.2 line crossover valve), 103
(No.2 line pumproom bulkhead valve),
142 (No.2 pump suction block valve),
143 (No.2 line suction/fill to slop tanks), 111 (port slop tank suction
fill valve).
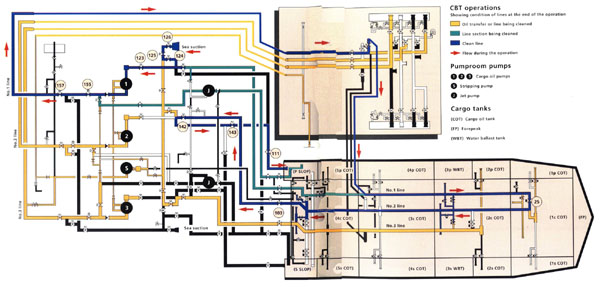
It should be noted that step 7 opposite is closely
related to the old practice of taking ballast into cargo tanks. If the
line flushing operation has not been properly conducted it also offers
the same opportunity to create a pollution incident. Since the flushing
operation is to a slop tank containing a quantity of water, there is
a possibility of back flow when the sea suction valve is opened. The
starting of the pump must be closely coordinated with the opening of
the sea valve to minimise the opportunity for outflow through the sea
suction.
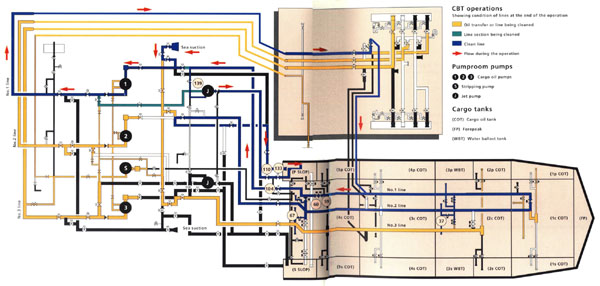
7 Open valves:
59, 60 (No.1 line block valves),
104 (No.1 line pumproom bulkhead valve),
139 (No.1 line to pumproom suction crossover valve),
110 (jet pump discharge to slop and ballast tanks),
133 (port slop tank fill valve).
8 Start the No.1 pump.
9 Flush from sea via No.1 pumproom
riser, deck line, deck drop, pumproom suction line, port jet pump, to
port slop tank. Flush for three minutes.
10 Stop No.1 pump.
11 Close valves 104, 139, 110,
133.
12 Open valves: 37
(No.1 centre tank main suction valve), 67 (No.4 centre ballast tank
main suction valve).
Inspect No.2 centre and No.4 centre ballast tanks for presence of oil
visually and with a hydrocarbon vapour tester, if oil is present tanks
must be emptied and ' washed to slop tank and flushing sequence repeated.
If tanks are free of oil, ballasting may proceed.
8. Ballast No.2 centre tank and No.4 centre tank
from sea via No.1 line:
1 Open valves:
58 (No. line to No.4 centre tank suction and fill),
67 (No.4 centre tank suction and fill valve), 41, 40 (No.1 line to
No.2 centre tank block valves), 37 (No.2 centre tank suction and fill
valve),
2 Start No.1 pump.
Ballast CBT tanks as directed.
2.2.4 MANAGEMENT CONTRIBUTION TO POLLUTION-FREE
CBT OPERATIONS
The amount of detail involved in the CBT procedures (see section 2.2.3),
clearly illustrates the complexity of CBT operations and the necessity
for adequately trained crews using clear, step-by-step operating procedures
and checklists. Also obvious is the number of opportunities for something
to go wrong! Despite the original intention for CBT to be an interim
measure, it remains a 'permanent' ballasting procedure for many ships.
For those vessels, management must insure that 'foolproof CBT directions
are provided to the crew. Carefully prepared CBT directives illustrates
management due diligence. If the crew uses photo copies of the procedures
as a checklist, and enters the date and time when each step was performed,
then due diligence in the performance of the procedures can be proven.
If a pollution does occur, evidence provided by the procedures and the
completed checklist will help to minimise any penalty.
2.2.5 Ballast records
All details of ballasting operations must be recorded in the oil record
book. Dirty ballast operations are also recorded in the port log. The
deck log book is used to record:
Dirty ballast taken on in port.
Dirty ballast taken on in river or sea.
Clean ballast taken on.
Dirty ballast discharged at sea.

Oil record book entry for CBT ranker.
All entries must include the times, tanks, and pipelines used for
the ballasting operations, and the vessel's positions at the time of
ballasting.
|