2.9 TANK WASHING PLAN
The requirements for tank washing during the ballast voyage are determined
primarily by the cargo orders for the next voyage and the cargo previously
carried. When the prior cargo is compatible with the next cargo to be
carried, tank washing may not be required. At the other extreme, if
a clean product voyage follows a black oil cargo then preparation may
require extensive tank washing, cleaning and even drying before the
tank is ready for the next loading. Other reasons for tank washing include
preparations for clean ballast, maintenance cleaning (to prevent sludge
accumulation), leak detection, tank or piping repairs and shipyard cleaning.
Between 1/4 and 1/3 of the ship's tanks may be washed for the reasons
above. In laying out his tank cleaning plan the chief officer considers
cargo requirements, ballast, repairs and maintenance. The most efficient
program is one which cleans as many tanks as possible for more than
one purpose. For example, if the chief officer has the choice of cleaning
and de-scaling one of two tanks for a cargo change, one of which has
been recently inspected, he should clean the other tank so that it may
be inspected during the de-scaling operation. Tanks which were crude
oil washed require water washing before they can be filled with 'clean'
ballast.
2.9.1 Tank preparation matrix and instructions
A time charterer may be responsible to the cargo owner for the adequate
preparation of the ship's tanks to receive cargo, but the owners and
master are ultimately responsible to charterer for the condition of
the ship's tanks for each voyage. The most important tool for setting
out the tank washing program is the tank washing matrix or cargo change
matrix. The tank washing matrix is a grid diagram with the 'previous
cargoes' arranged in horizontal rows and the 'next cargoes' listed as
vertical columns. By finding the intersection between the column corresponding
to the last cargo carried and the row headed by the next cargo to be
loaded, the chief officer can determine the tank preparation requirements.
Tank washing matrices should be provided for both coated and un-coated
tanks, as the required preparation is somewhat different. Coated tanks
with coating failure of more than 10% of the total surface should be
considered and washed as un-coated tanks.

This table is an example of a cargo tank preparation
matrix for use on clean product tankers. The recommendations are examples
only, and should not be used for guidance when owner's or charterer's
tank cleaning instructions are available.
The origin of a tank preparation matrix is the amount of maximum allowable
contamination between products which can be permitted while maintaining
product quality. Cross contamination between products can affect a number
of product criteria such as:
Colour, octane, density, bromine number, lead, sediment, cloud point,
flash point, vapour pressure, viscosity, gum, sulphur, thermal stability,
odour, pour point, smoke point, carbon content, final boiling point,
initial boiling point, water separator index, mercaptan.
It would be difficult for a chief officer to evaluate each of these
criteria when changing cargoes. Owner's have done this for him by preparing
standard tank washing matrices.
The levels of preparation indicated may include:
No cleaning required
Drain lines and pumps
Hot water machine wash
Ventilate tanks
Remove all sludge and scale
Mop and ventilate tank
Number of washing cycles |
Bottom flush and strip dry
Cold water machine wash
Fresh water rinse
Gas free tanks
Remove all free water
Cleaning impractical
Number of washing hours |

The table above is an example of a cargo tank preparation
matrix for use on black oil tankers. The recommendations are examples
only, and should not be used for guidance when the owner's or charterer's
tank cleaning instructions are available.
The required preparations may include any one, or a combination of
the above procedures. The most stringent preparations are required for
refined products, but some mixtures of crude oils can be equally troublesome.
Some combinations of crude oils can form nearly impervious residues
and some crude oils with special properties, such as nil sulphur, can
be contaminated by other crude oil residues.
In every case where a tanker is instructed to load a cargo different
from the previous cargo, cleaning instructions must be provided with
the orders. The instructions may be a simple as 'charterer's minimum
cleaning requirements to be completed', thereby referring the master
to the charterer's printed instructions and a tank cleaning matrix for
tank preparation. Alternatively, the preparation may be a page of detailed
steps. If the master or chief officer has any question about the necessary
tank preparation, then the owners must be consulted for clarification.
Example tank preparation matrices are included in this section. It is
important that the master and chief officer follow the procedures required
by the owner/charterer for tank cleaning. If a special circumstance
arises which is not covered by the instructions, or which requires special
measures, then the situation must be communicated with owners/charterers
and the tank(s) cleaned according to their reply.
Tank inspections at the loading port may be performed by independent
inspectors (representing the charterer or cargo owner), or by terminal
inspectors. Masters should always give serious consideration to the
advice of these inspectors and should develop a habit of consulting
with them. If a disagreement develops regarding suitability of tanks
for loading, then it must be referred to the cargo owner and owner/charterer
for resolution. The master may wish to request a surveyor to examine
the tanks on the vessel's behalf to determine tank suitability. On more
than one occasion, ship's tanks have been rejected by loading terminal
representatives because the cargo was not available for loading, or
the cargo was so marginally on-specification in the shore tanks that
it could not be loaded into any vessel without being put off specification.
Part of the function of the tank cleaning matrix is to ensure that excessive
or unnecessary tank washing is not employed. Excessive cleaning wastes
time, energy and accelerates tank structure or coating deterioration.
In the final decision of the level of cleaning to employ, the chief
officer and master must take into account the condition of the ship's
tanks and any special considerations relating to the cargo which they
are made aware of.
For crude oils, the following guidance is provided:
General crude oil trading
Normally, cleaning is not necessary between different types of crude
oils, or between successive voyages. All tanks should be re-stripped
to the slop tank after the vessel has departed and reached warmer waters.
This step alone will recover most of the residual cargo in the tanks.
Crude oil residues may be the most difficult to wash from the cargo
tanks. They combine the high hydrocarbon vapour characteristics of gasoline
cargoes with a potential for leaving sediment and wax. Sediment must
not be allowed to accumulate in the tanks. If heavy sediment was noted
on the previous discharge report, the tanks should be bottom washed
and checked for proper drainage. On trades involving crudes with heavy
sediment, frequent washing of all cargo tanks will be necessary to control
the accumulation in tank bottoms. Alternatively, lighter crudes without
sediment will require little or no tank washing between cargoes. Tanks
which have been crude oil washed require little water washing to prepare
them for clean ballast and limited ventilation before entry. When it
is important to minimise washing water volumes (ie. when slop disposal
ashore is required), then all tanks scheduled for water washing should
be crude oil washed at the discharge port.
Salt water contamination of crude oils
Salt is a contaminate of crude oils. It is important to have crude tanks
as dry as possible before loading. This is particularly true if the
specific gravity of the oil is high, ie. near to that of water. Salt
water is difficult to separate from heavy crude oils and it can cause
significant problems in the refinery. Some crude oils requiring particular
care in this respect are:
Boscan
Tia Juana
Bachaquero virgin gas oil
Preparation of tanks for these and similar crude oils should be conducted
as follows:
a Hot water wash tanks to remove all loose scale, sludge
and sediment.
b Flush the entire cargo system with fresh water.
c Strip tanks dry prior to loading and drain all lines
and pumps.
d Blow lines with air or inert gas.
e Give all tanks a fresh water wash.
f Drain and blow down lines a second time.
If shore lines are to be displaced to the ship, they should all be received
into a single tank. Any slops from the previous voyage should be segregated.
After loading, check each tank for water and record the results. If
excessive water is found, give a letter of protest to the loading terminal.
Crude oils with API's near to that of water (API = 10.0)
a Drain all tanks as thoroughly as possible to remove
the remains of the previous cargo. A bottom flush or bottom wash is
also recommended. Tanks containing heavy deposits of sediment and scale
should be gun-cleaned with water.
b Remove all scale /sediment. If tank entry is involved,
tanks must be gas freed and rendered 'safe for men and fire'. (See section
2.15 for tank entry procedures.)
c After discharge of ballast at the loading port,
and the thorough stripping of tanks and cargo lines, drain all cargo
pumps and pipeline systems.
d Purge pumps and lines with compressed air or inert
gas, giving due consideration to the relevant safety regulations in
force.
e Test all heating coils to make sure they are in
good operational condition.
Cutback asphalt
a Since water is a critical contaminant of this cargo,
it is essential that no water remains in the cargo system. The entire
cargo system to be used for asphalt should be given a line and tank
flush with fuel oil prior to loading. If detailed charterer's instructions
are not provided, then proceed as follows:
b Arrive with tanks free of residues and gas free.
Strip the tanks, lines and pumps as dry as possible. Cargo systems (lines,
pumps, and strainers), must be drained, then blown dry. All cargo valves
must be opened and drained to the cargo tanks. The tanks must be free
of pumpable water.
c At the loading terminal, set the lines for loading
and load 200 to 400 barrels of flushing oil into each cargo tank. Then
transfer the oil from tank to tank , using the ship's cargo pumps, until
all tanks have been flushed. Dispose of oil (ashore or co-mingle with
other fuel oil), according to charterer's or owner's instructions.
Crude condensate
Ras Tanura loadings - special problems
Some crude oil condensate which has a Naphtha base can form chemical
compositions when loaded into cargo tanks that previously contained
crude oil. This occasionally results in the presence of large quantities
of un-pumpable asphalt residues at the discharge port. These residues
are derived from the interaction of the condensate with the ROB from
the previous crude cargo. Asphalt cannot be removed by ordinary cleaning
methods, so the cleaning is very expensive. Therefore, naphtha base
condensate should never be shipped in unclean tanks containing crude
oil ROB.
When condensate is loaded on top of crude oil, or if being topped up
with crude oil, the concentration of the lighter component should not
exceed 10% by volume of the total crude/condensate mixture. This arrangement
must be agreed between owners/shippers/ charterers prior to loading,
because:
a A higher concentration may cause a significant
fallout of heavy, high boiling hydrocarbons, making it impossible to
drain the tanks at the cargo port.
b If a richer mixture is shipped, the high vapour pressure
of the cargo may prevent the use of crude oil washing in the discharge
port, as the P/V valves will lift. Higher tank pressures will prevent
IGS from properly flowing to the tank. Such cargoes should only be carried
in SBT vessels.
Crude oils to be used in the manufacture of lube oils or asphalt
a Gun clean all tanks with hot water - one full cycle.
b Thoroughly flush all pumps and pipelines with water
and pump as dry as possible.
c Remove all sediment, loose scale and sludge from
tank bottoms. If tank entry is required, tank atmosphere requirements
for 'safe for men; safe for hot work' must be met.
d Rinse the entire cargo system with fresh water.
If time allows, give all tanks a fresh water rinse.
e Strip all tanks as dry as possible. Drain all water
from pumps and pipelines prior to loading. Remove cargo piping drain
plugs and pump drain plugs during pre-loading inspection at the loading
berth.
Fuel oil/'black oil' cargoes
Thorough draining is required when changing from crude oil to fuel oil,
or from a fuel oil with a higher number to one of a lower number, such
as from No.6 oil to No.4 oil.
Draining is not required when changing from a fuel oil with a lower
number to one with an equal or higher number.
Accumulation of sediment noted on a discharge report is an indication
of the need for bottom washing of black oil cargo tanks.
Absence of cargo preparation orders
If cargo loading orders have not been received at the time the ballast
voyage begins, the ship should perform only the minimum necessary preparations,
including:
• Flush tank bottoms with water and strip flushings to the slop tank.
• Wash pumps and pipelines to the slop tank.
• Wash necessary tanks for clean ballast (if required).
• Load clean ballast (if required).
• Decant dirty ballast, stripping residues to slop tank in accordance
with MARPOL requirements.
• Flush pumps and pipelines to the sea.
2.9.2 The pumpman and deck crew
The tank washing operation requires the closest cooperation between
the chief officer, pumpman, and the deck crew to operate efficiently
and obtain the required result. The best results will be obtained if
the chief officer prepares a preliminary plan and discusses the plan
with the pumpman and boatswain. The plan should be detailed enough to
indicate the times of starting and finishing the washing operation in
each tank and the sequence of tanks to be washed.
It is not unusual for the pumpman to have completed more tank washing
operations on the vessel in question than the chief officer. In that
case, his assistance is invaluable with respect to knowing how well
the stripping pumps or eductors work, how well the tanks will drain
and which tank washing machines may present problems. Problem tanks
should be scheduled for daylight hours; easy ones can be done at night.
The deck crew may be able to offer suggestions on handling of the portable
tank washing machines, such as where they have been known to become
entangled in tank structure when the ship is rolling. Including the
crew in the planning of the job makes them more interested in seeing
it done well. With proper planning and scheduling, an experienced crew
is capable of conducting all of the mechanical aspects of the tank washing
operation with minimal, general oversight by the chief officer.
When the chief officer has reviewed his plan with the pumpman and crew,
he adds the final details, then discusses it with the master. The final
plan should include both a diagram of the program and a detailed schedule.
On the diagram, mark the time each tank will start, the times of program
changes, or portable machine 'drops' and the time it will finish. Allow
sufficient time between tanks for stripping. Indicate the time when
tanks may be sounded to measure residues (not less than 30 minutes after
finish washing and only with a grounded probe). When the master has
approved the plan, copies are distributed to the watch officers, chief
engineer, engine control room, pumpman, boatswain and one copy is posted
on the crew's (company), bulletin board.
With the program set out in advance, the chief officer is free to concentrate
on verifying the safe conduct of the operation, checking the operation
of fixed or portable machines and ensuring that the next tank is set
up for washing before the previous tank is finished. His primary objective
is the safety of the crew. This is particularly important when washing
with portable machines. The portable machines are heavy, and there are
many opportunities for the crew to create hazardous static electricity
conditions if their actions are not properly monitored and correct procedures
followed. When washing with portable machines, the crew is exposed to
the dangers of broken feet and hands, hot water burns and tank explosions.
The crew must be carefully instructed in safe work practices and provided
with the necessary protective equipment of prevent injury. All personnel
on board should be notified that tank washing operations are to commence
and that all safety precautions as when loading must be observed.
A basic tank diagram chalkboard should be set up on the main deck (one
may be conveniently painted on the side of the superstructure near the
pumproom). The tank washing plan is marked on the chalkboard. The deck
watch marks the chalk board to reflect the current progress of the tank
washing.
If the tank washing program is extensive, or the ballast voyage short,
the tank washing operation should be started immediately after dropping
the outbound pilot and continue nonstop until it is completed. Three
or four men are required in each hose handling operation, so the watch
and crew rotation will need some careful consideration. Handling the
heavy machines and hoses repeatedly for eight to twelve hours at a time
is demanding work.
2.9.3 Tank washing machines
Portable machines
When tankers were smaller and crews were larger, all tankers were cleaned
with portable tank washing machines. Portable machines are connected
to the end of a special tank washing hose. The machines have a bronze
body and the hose couplings are bronze. The hoses are marked at intervals
of five feet or two meters. A natural fibre line must be attached to
the machine for support and ease of handling, even though the hose is
fully capable of supporting the machine unaided. The other end of the
hose is connected to a hydrant on the deck tank washing line or fire
line. The water should be started and the hose flushed through before
the machine is placed in the tank. The machine is then lowered into
the tank through a tank washing opening and supported by a 'saddle'
placed over the opening. The hose is clamped into the saddle and the
machine tether line is made up on the saddle clamp to support the machine.
Tank washing openings are strategically placed in the main deck to permit
good coverage of the tank's inner surface without permitting the machines
to become entangled in the tank's internal structure. The tank cleaning
openings are normally covered by bolted circular covers with gaskets.
The bolts are removed from all the plates to be used, but the plates
should be kept in place until a machine is ready to be inserted into
the opening and the plate replaced promptly after the machine is removed.
The distance the machine is lowered into the tank depends on the size
of the tank and the amount of washing required. For heavy cleaning,
the machine may be placed at three or four successive levels ('drops'),
depending on the complexity of the tank structure. Each drop should
be just above one of the main structural members, so that the upper
surface of these side longitudinals or transverse members are thoroughly
cleaned. If the cargo tank is known to have a heavy accumulation of
sediment, the machines should be lowered to the bottom first and washed
for ten minutes to clear the limber holes of sediment, then raised to
begin the normal wash.
At each level, the machines are operated through a full washing cycle.
The cycle time is determined by the washing pressure. When all machines
are ready, the engine room is asked to start up the tank washing pump
and if necessary the tank washing heater. Sea water is pumped at high
pressure from the engine room, through the heater (if required), into
the deck washing or fire line and into the tank washing hoses. The force
of the water passing through an impeller in the machine causes the offset
nozzles to rotate in a vertical plane and the whole machine to rotate
in a horizontal plane. The jets of water from the nozzles trace a pattern
on the inside of the tank which provides effective coverage of the entire
surface within range of the jets. The maximum range of the jets is normally
nine to ten meters. The washing pattern described by the dual nozzle
rotation resembles a ball of twine.
Cycle times for the washing machines are a function of nozzle size and
washing water pressure at the machine. The pressure at the machine will
be lower than the pressure at the pumproom or in the engine room. The
only way to accurately measure the pressure is to have a portable gauge
fitted to the wash water supply line on a spare tank washing outlet
near the machine hose connections. A typical product carrier tank washing
machine with 12 mm nozzles will have a cycle time of 38 minutes at 5
kg/cm sq. (75 psig) and a cycle time of 28 minutes at 12 kg/cm sq. (175
psig).
Higher pressures will produce higher flow rates. The same product carrier
machine will use 20 tons of water per hour at 5 kg/cm sq. and 30 tons
per hour at 12 kg/cm sq.
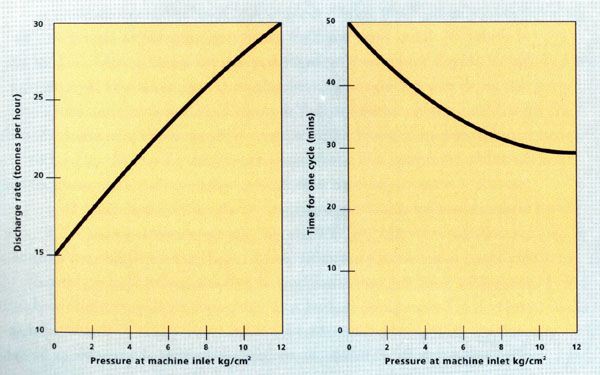
Example performance curves of a portable tank
washing machine.
For effective tank washing the number of machines used at one time
must not put more water into the tanks than the stripping pump is capable
of removing. By referring to the discharge rate curves for the machines
on his ship, the chief officer can determine the maximum number of machines
his stripping pumps can keep up with.
Complete coverage of the tank surface may not be possible with machines
lowered through the dedicated tank washing openings. It may be necessary
to lower a machine through the tank hatch, or to actually enter the
tank and tie off a machine in a corner of the tank to remove accumulations
in hidden corners. Confined space entry procedures must be used!
It is a good idea to leave the main cargo suction/fill valve open while
the tank is being washed, to drain any residual cargo from the branch
line into the tank. If clean ballast is to be loaded, each tank should
receive a short flush from the sea immediately before or when starting
the washing operation.
Fixed machines
Tank ships larger than 60,000 tonnes are difficult to wash effectively
with portable machines. The number of deck openings required to provide
adequate coverage and the depth of the tanks would require a long and
strenuous effort which today's smaller crews are not capable of supporting.
Tank washing capability for these larger tankers is provided by fixed
tank washing machines, sometimes referred to as 'guns'. Fixed tank washing
machines are mounted on the deck of the ship with control machinery
outside the cargo tank and the rotating parts and spray nozzle inside
the tank. Fixed washing machines are capable of higher washing pressures
and longer effective reach than the portable machines. On crude carriers,
they are carefully placed to provide a washing pattern which covers
the maximum amount of the tank surface by direct impingement of the
washing stream. In accordance with IMO COW system requirements (section
4.2.8), the shadow areas of the tanks
shielded from direct impingement cannot exceed 10% of the tanks horizontal
surfaces and 15% of vertical surfaces. The washing sequence of the cargo
tank is programmed into each machine, depending of its location in the
tank. A tank cleaning operation with fixed machines requires only that
the machines be set to the correct starting position and operated in
the correct order, to provide a complete cleaning of the tank. The fixed
machines can be used to crude oil wash (COW), or to water wash the cargo
tanks, according to the purpose of the washing. Because of the static
electricity hazards of high-capacity tank washing machines, they must
only be operated in properly inerted tanks (see section 2.10.3).
2.9.4 Washing pressures, temperatures and times
The tank washing operation consumes energy and time and erodes the tank
coating or tank structure. It is important that the washing be thorough
enough to properly prepare the tank(s) for the next cargo, but not excessive.
Washing tanks with too high pressure or temperature, or for excessive
time will not improve the result and may cause coating or steel deterioration
which, if repeated often enough, eventually becomes significant damage.
Maximum tank washing pressures are often dictated by the capacity of
the tank washing pump. Higher pressures will reduce machine cycle times
and the overall tank washing time. High pressures will produce a more
thorough cleaning. Washing pressure of 12.6 kg/cm sq (180 psi), is most
desirable for washing crude or fuel oils from un-coated tanks. For washing
clean product tanks, pressures of 9 to 10 kg/cm sq (130 -140 psig) are
suitable. Washing pressure must be maintained below the maximum allowed
for the tank coating material in coated tanks. To properly measure the
tank washing pressure, a gauge must be fitted in the tank washing line
near to the machine connection. Chief officers should refer to the owner's
operating instructions to determine maximum washing pressures. If no
guidance is provided, it should be requested from the owners.
Unless there is a special requirement, tanks should be washed with cold
(ambient) sea water. Cold water washing will normally leave behind only
a waxy skin, which provides a protective film for the steel. Tepid water
(between 30 and 65 °C), is of no practical benefit since it has the
disadvantages of both hot and cold water without providing the benefits
of either.
Maximum tank washing temperatures are often dictated by the capacity
of the tank washing heater and the number of machines in use. Higher
temperatures will increase the effectiveness of difficult washing situations.
Washing temperature must be maintained below the maximum allowed for
the tank coating material in coated tanks. Modern coatings which have
been correctly applied to properly prepared surfaces should have no
washing water temperature limitation and some charterers will not accept
any. If maximum permitted temperature information is not available for
a ship with coated tanks, then use an upper limit of 120 °F (49 °C).
Special caution is required if a coated tank to be washed has carried
a product (such as benzene or toluene), which can soften the coating.
Such tanks should not be cleaned until the coating has 'cured' after
the discharge of the cargo. To properly measure the tank washing temperature,
a thermometer may be fitted in the tank washing line near to the machine
connection, or a bucket filled from the washing line and the temperature
measured by dip thermometer. Chief officers should refer to the owner's
operating instructions to determine maximum washing temperatures. If
no guidance is provided, it should be requested from the owners.
Tank washing times must be calculated based on the washing pressure
at each machine. For portable machines, the tank should be washed until
the machine with the lowest pressure has been able to complete the full
cycle. The portable machines may then be lowered to the next 'drop'
level. Only by permitting the machines to complete their full cycle
is complete washing ensured. Portable machines are usually left at each
drop for a complete cycle, but may be operated at the lowest drop for
two cycles to remove heavy residue or scale accumulation from the tank
bottom.
It is important to check the position indicators on fixed machines to
ensure that they have completed their cycle before stopping the flow
and starting the next machine.
2.9.5 Handling portable tank washing machines
and hoses
Portable tank washing machines and hoses are rugged, precision equipment,
which require proper care and handling to provide safe and effective
performance. Machines should never be dragged along the decks; the best
way to move them from storage to the tank washing area is by use of
a hand truck. They should not be used in tanks with complex structure
while the ship is rolling. The rolling may cause the machines to strike
tank framing; this could damage the machine, damage tank coating and
cause dangerous sparks. The portable machine should be fitted with a
natural fibre line of up to 16 mm diameter. This line is used
to lower and retrieve the machine from the tank, instead of lowering
and pulling it out by the hose. Machines should be flushed with fresh
water after use and dried or given a coating of oil according to the
manufacturers instructions. The pumpman should be given training to
properly maintain the machines and an adequate supply of spare parts
to do so.
Tank washing hoses should be drained and stored in a protected area
between washing operations. Tank washing hoses couplings should be tightened
and disconnected from the washing main using wrenches only, (not hammered
on). Regular replacement of the washers will prevent leaking. To prevent
static electricity hazards, the hose bonding wire continuity must be
verified before each use and the hoses must remain connected to the
washing main at all times while the washing machine is in the tank.
2.9.6 Tank coating protection
Modern epoxy tank coatings are tough and resistant to all of the cargoes
and tank washing procedures to which they would normally be exposed.
However, there are limitations associated with each coating and it is
important that these limitations be readily available to the chief officer
and that he ask for clarification of any questionable circumstances.
For example, certain types of coatings are not approved for carriage
of some jet fuels. Both the coating and the cargo will be damaged by
loading such fuels into the coated tanks. Coatings are also subject
to damage by washing with too high temperature and/or too high pressure
water. To prevent such damage, the pressure and temperature limits should
be readily available to the chief officer and posted at the tank washing
heater/pump in the engine room. The chief officer must remember that
a ship's tank coatings represent a significant portion of the overall
cost of the ship and require his diligent care to protect them from
damage.
2.9.7 Washing with detergents
Detergents should be used only when absolutely necessary. They are normally
applied to difficult tank washing situations, where absolute purity
of the next cargo is required. They are injected into the tank washing
line by a mechanical pump, mix with the washing water and act along
with the water jet to remove the previous cargo clingage and residue.
When using detergents, the chief officer must:
Ensure that the personnel using the chemicals are adequately trained
regarding their hazards and that necessary personal protective equipment
is made available.
Verify that the detergents may be safely used with the tank coatings.
Advise the owner/charterer that the ship will arrive at the loading port
with tank washing slops containing detergent.
Detergents are harmful or poisonous to marine life and should not
be discharged overboard. The presence of detergent in the wash water
increases the potential for static electricity accumulation. To avoid
dangerous accumulations of static electricity, used wash water containing
detergent should not be recirculated from the slop tank for tank washing.
Many loading terminals will not accept slops containing detergents.
For that reason alone, detergents should not be used unless absolutely
necessary.
2.9.8 Washing bunker tanks
Washing bunker tanks is not normally required except to remove contaminated
bunkers, or to clean the tank for repairs. Bunker tanks are not usually
set up with the necessary tank washing openings and the draining of
wash water must be accomplished with the bunker transfer pump. For these
reasons, bunker tank washing may require even more planning than a normal
cargo tank washing. Hoses must be rigged to transfer the wash water
from the bunker system to the cargo stripping system. Since the bunker
tank opening may be in the engine room, special ventilation or ignition
control procedures may be needed to ensure that there is no opportunity
for an explosive atmosphere to be created and ignited.
2.9.9 Inert gas system and vent lines
Part of cleaning a tanker for repairs or shipyard period involves washing
out all tank vent lines and inert gas lines. Even if cargo has not entered
these pipelines as a liquid, cargo vapours are liable to condense in
the lines and form accumulations of hydrocarbons. Cargo tank vent lines
are fitted with washout connections permitting them to be flushed back
to the cargo tank before the cargo tank is washed.
The same flush-out connections are fitted to the IGS line. A tank washing
hose should be connected to each flush-out connection and the branch
lines flushed either into the cargo tank (before tank washing) or back
to the deck non-return valve, from which they must be pumped or drained
to a cargo tank.
2.9.10 Steaming tanks
Steaming cargo tanks produces large accumulations of static electricity.
For that reason, steaming should only be done in inerted tanks.
|