5.28 STRIPPING CARGO
The strategy employed in completing the discharge of cargo will determine,
to a large degree, the impression the charterer and the facility will
have of the ship's performance. A carefully planned and competently
completed tank stripping (draining), operation will ensure a minimum
discharge time and maximum cargo outturn. A full knowledge of the characteristics
of the cargo and the capabilities of the ship's pumping systems are
essential to achieve maximum outturn with minimum time in berth.
5.28.1 Types of stripping systems
A tanker may have a stripping system made up of independent suction
piping, or it may have alternative stripping suction outlets from the
main cargo lines.

Simplified diagram of suction piping with an independent
stripping system.
The first alternative is the most versatile and permits the earliest stripping
of tanks after they have been emptied as far as possible by the main cargo
pumps. To use a stripping system off the main cargo lines, the main pumps
must be either finished their work or stopped. This will tend to delay
the discharge.
Stripping suction valves in tanks should be 'globe/check' valves, a special
type of valve which acts as a non-return valve when opened only a few
turns, but permits full flow when fully opened. These valves are opened
fully when stripping begins, then closed to the check position as the
tank becomes nearly empty.

Simplified diagram of suction piping with main
and stripping lines combined. One pipeline
system has both main (large diameter) and stripping (small diameter)
suctions.
Some stripping systems are fitted with 'last litre' (or 'last gallon')
suctions, small diameter suction lines connected between the stripping
suction valves and a stripping suction block valve. When the tank appears
to be empty, the stripping suction valve is closed, leaving the block
valve open. The pump then draws through the 'last litre' line suction
located in the very corner of the tank a few millimetres above the tank
bottom.
Either type of stripping system will normally have two stripping pumps
in the pumproom, arranged so that they can be used simultaneously and
separately on different groups of tanks.
The stripping discharge piping will include lines to the midship manifold,
to the slop tank(s) and possibly to an aft cargo tank which can be used
for a stripping accumulation tank. There may also be a stripping overboard
discharge line. The overboard valve(s) must be verified to be fully
closed and sealed before the stripping pumps are started.
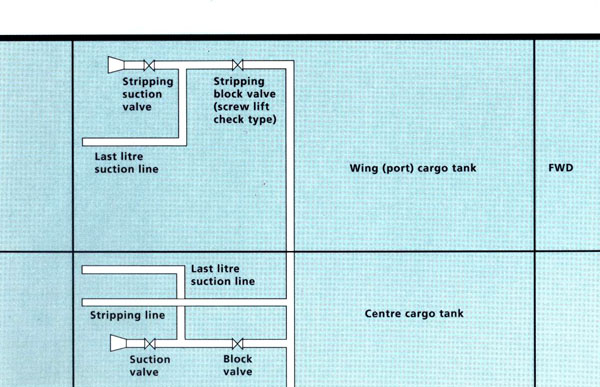
'Last-litre' stripping line used for maximum recovery
on product tankers. When the suction valve
is closed, with the block valve open, the stripping pump suction acts
on the small-diameter line, achieving maximum cargo recovery.
5.28.2 Stripping pumps
Most stripping pumps are based on an operating principle called 'positive
displacement'. The oil which enters the pump is mechanically moved from
the suction side to the discharge side. This action creates a vacuum
at the suction side of the pump, enabling the pump to 'lift' cargo from
the tank into its pumping chambers.
The typical positive displacement pump is a reciprocating pump, normally
of duplex (two pumping chambers), double-acting design. The internal
mechanism is designed so that the cargo piston pumps on both the upstroke
and the downstroke. The key components to the proper function of reciprocating
pumps is the condition of the internal cargo valves. These should be
examined regularly to ensure that their springs and seating arrangements
are in good order.

Duplex reciprocating pump.
Reciprocating pumps are steam powered. To reduce the hazard from hot
steam lines in the pumproom, the lines must be completely and tightly
insulated to prevent vapourisation or ignition of any cargo leaks which
could spray or flow onto them.
A second type of stripping pump is a rotary or gear pump. These usually
consist of two meshing gears which move the cargo between the pump casing
and the gear teeth as the gears are rotated. These pumps are usually
powered by an electric motor. They are very efficient and particularly
suited for pumping high viscosity oils, such as lubricating oils or
molasses.
A third method of stripping tanks does not use a pump at all, but a
device called an eductor. The eductor obtains its vacuum or 'lift' by
use of a drive fluid, normally the stream of cargo from the main cargo
pump discharge. The principal advantage of the eductor is that it cannot
lose suction or be damaged by being run dry. The disadvantage is that
once the main cargo pump is stopped, there is no drive fluid available
and no further stripping is possible.
5.28.3 High-pour cargo
Effective stripping of high-pour-point cargo begins with achieving the
correct cargo discharging temperature. The cargo must be heated to and
maintained at the recommended discharge temperature until the cargo
surface reaches the level of the heating coils. (Steam to the heating
coils must be shut off just before they are exposed by the receding
cargo.)
Tanks must be discharged systematically, so that a stripping pump is
immediately available when the tank is at minimum main cargo pump level.
It is usually desirable to line up and start the stripping pump before
the main cargo pump is switched from the tank, so that the stripping
pump is already working when the tank reaches the stripping level. Each
tank should be stripped as dry as possible, then re-stripped two or
three times at thirty minute intervals.
If the shore requests a discharge stop before stripping is complete,
protest the delay, indicating that it will increase the vessel's ROB.
If the stop is essential, the best course is to begin stripping to an
accumulation tank. If sufficient strippings can be accumulated to cover
the heating coils in the accumulation tank, cargo heating can be resumed.
After all tanks have been stripped, recirculate cargo via the deck discharge
line and loading drop to prevent line blockage until discharge ashore
can be resumed.
It is particularly important to arrange for effective COWing of waxy
crude oils so that the tank bottom wash occurs as soon as possible.
If this is not done, the formation of wax in the cooling oil will block
the limber holes, preventing the flow of cargo to the tank suction inlet.
The following crude oils are known to congeal rapidly as their temperature
approaches the pour point, so rapid stripping is essential:
Cargo |
Origin |
Discharge temperature °C |
Pour point °C |
Bahia |
Brazil |
60 |
24 |
Cabinda |
Angola |
33 - 44 |
27 |
Gamba |
Gabon |
32 |
16 |
Midas Crude |
Indonesia |
52 - 57 |
35 |
Rio Zulia |
Columbia |
44 - 49 |
27 |
San Juaquin |
Venezuela |
41 |
24 |
Sarir |
Libya |
38 |
21 |
Zeta North |
Venezuela |
38 |
21 |
Daquin Crude |
China |
52 |
32 |
It is essential that tanks with these cargoes be immediately drained
after they have been drawn down to the bottom longitudinals.
If the best efforts of the stripping programme do not prevent heavy
clingage of un-pumpable ROB, then the only recourse is to back-load
500 to 1000 tonnes of light crude oil or light gas oil into the slop
tank and closed cycle COW with this wash oil until the ROB/ clingage
has been reduced to an acceptable level. After washing, the slop tank
is measured to determine the gain from COWing and then discharged ashore.
After completion of high-pour cargo discharge, immediately circulate
hot water (74 °C), through all deck lines, pumps and risers, stripping
all water and residue to the slop tank.
5.28.4 Stripping high vapour pressure cargoes
Stripping high vapour pressure cargo requires pumps that are in good
mechanical condition and are carefully operated. Pumps should be operated
at slow to moderate speed, else the rapid piston action of the reciprocating
pumps will tend to 'flash' the cargo in the cylinder, forming vapour
or gas. The vapour or gas reduces the effectiveness of the pump and
may cause it to lose suction entirely be becoming vapour bound. It is
particularly important to keep enough cargo in one tank for priming
the pumps when stripping high vapour pressure cargo.
Keep stripping pumps separated; making their suction lines common increases
the tendency to become vapour bound. The discharge valve of the pump
may be closed slightly to provide additional back pressure to improve
pump performance.
Increasing the inert gas pressure in the tanks being stripped will increase
the effective positive suction head in the tank and reduce the tendency
to cargo vapourisation, however if COWing is being performed it will
add additional pressure to the tank, which could cause the pressure
relief valve to lift.
5.28.5 Accumulation tank
Cargo tanks can be stripped most efficiently when the ship is discharging
a single cargo. As the tanks are emptied by the main cargo pumps, they
can be stripped to an accumulation tank, which in turn can be discharged
with the higher capacity (centrifugal) main cargo pump. When stripping
to an accumulation tank, it is important that the tank be discharged
to between 1/2 and 2/3 of total depth before stripping begins. This
provides space to receive strippings.
The ullage of the accumulation tank must be carefully monitored to avoid
an overflow. One method of avoiding this is to slightly open the accumulation
tank main suction valve to an active cargo pump. This will keep the
tank at about the same level while stripping and will help to keep the
main cargo pump primed.
5.28.6 Shore back-pressure
Shore back-pressure is occasionally so high that it is very difficult
or impossible for the stripping pumps to move the final cargo residues
ashore. Port Jefferson, New York is a good example of this. The 60 psi.
of shore back-pressure there can only be overcome by stripping pumps
in top condition.
To overcome high shore back-pressure, the best recourse is to use a
stripping accumulation tank on board to receive all of the tank strippings
and all of the pipeline drainings except for one discharge line. The
accumulation tank should be at least 14 filled when finished. If necessary,
stop the discharge with the main cargo pump to retain that amount of
cargo. (Remember that outturn is more important than turnaround time!)
When all strippings have been accumulated, start the main cargo pump
on the last tank, discharging via a single cargo line to shore. Monitor
the MCP performance carefully, reducing its speed and adjusting the
pump discharge valve to maintain suction and discharge pressure as long
as possible. When the MCP loses suction, the stripping pump can attempt
to strip the remaining cargo in the accumulation tank ashore, followed
by the remaining cargo pipeline(s) stripped ashore via the small-bore
MARPOL discharge line, (see section 5.31).
5.28.7 Other stripping considerations
Stripping operations will be more successful if the ship is properly
trimmed and listed. The largest trim aft, acceptable within the vessel's
stress limitations, will provide the best draining of tanks. On a 240
meter vessel, four meters of trim aft represents only one degree
of slope to aid the flow of cargo to the suctions. One degree is ,not
much! More trim provides better draining! The ship should be listed
to port or starboard, or trimmed with no list depending on the location
of the tank suctions.

A Tanker with deadrise - ranks
are stripped with no list on the ship. B Tanker without
deadrise - port list required for effective stripping. Stripping suction
location depends on hottom design and desired list (port and starboard)
for best cargo recovery.
In some ships the tank suctions are located in the aft, port cornei
of each cargo tank. It is important that these ships be listed to port
when stripping to achieve the best drainage. Other ships have the stripping
suctions in the inboard corners of the wing tanks and at th centre of
the centre cargo tanks. These ships must have zero list for best stripping.
The cargo watch officer must know the suction locations in the tanks
and the chief officer should include stripping trim instructions in
the discharging orders. If a list is required for stripping, the aft
wing tanks should be retained to provide it. At the same time, the tanks
can perform additional service as pump priming tanks. Record the amount
of stern trim in the logbook every two hours while stripping.
Automatic ullage tape floats will tend to stick to the bottom of the
tank after discharging heavy or viscous cargo. Have the pumpman roll
up and secure the tapes immediately after stripping is completed.
The pulsating discharge pressure of reciprocating pump can occasionally
set up a harmonic oscillation in cargo transfer arms. The deck watch
should be instructed to watch for this and to advise the cargo watch
officer if it begins. The oscillation can normally be stopped by reducing
the speed of the stripping pump.
If stripping with an eductor system, use the smallest tank possible
to provide drive fluid for the eductor during the final stripping. This
final tank will have to be drained with the main cargo pump, making
complete draining unlikely. A No.l wing tank makes a good choice. With
the ship trimmed aft, it will have a good elevation above the pump and
the small bottom section of the wedge-shaped wing tank will have the
least volume/depth ratio of all tanks on the ship, leaving the least
cargo on board when the MCP loses suction.
If a charterer or terminal representative is on board, he should be
encouraged (or challenged), to witness and confirm that the stripping
operation was thorough and successful. This will, at the least, put
to the test his commitment and the authority of his position. It may
avoid the difficulties of proving effective stripping efforts and results
to the independent inspector at the final survey. Independent inspectors
will rarely undertake any form of initial survey (inspection before
completion of discharge), on behalf of their clients.
5.28.8 Stripping deepwell pumps
A well maintained and properly operated deepwell pump will drain a cargo
tank almost as dry as a reciprocating stripping pump. At the end of
the discharge there may remain a small amount of cargo in the tank and
the pump well will be full, or partially full, of cargo. Some vessels,
particularly chemical tankers, are fitted with small, air operated reciprocating
pumps in the tank adjacent to the deepwell. Using reach-rods from the
deck, the pumpman is able to first take suction from the tank bottom
with this pump, completing the stripping of the tank. Then he can open
a suction valve to the deep well and pump its contents (and in some
cases the contents of the discharge line), to the discharge manifold
via a small diameter line.
The small stripping discharge line is connected to the discharge manifold,
outboard of the manifold valve.
|